Our Products
LaserNet Fines
Particle Counter and Particle Shape Classifier
"LaserNet Fines was developed by Lockheed Martin Tactical Defense Systems in cooperation with the Naval Research Laboratory for the Office of Naval Research on its Accelerated Capabilities Initiative for Condition-Based Maintenance."
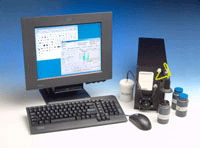 |
Application
Machine condition monitoring based on oil analysis has become an accepted practice in any well run maintenance management program. With prior knowledge of the wear metals and contaminants present in a lubricating system, it may be determined if that equipment is operating properly or if preventive maintenance is required. LaserNet Fines combines the standard oil analysis techniques of particle counting and shape classification into a single analytical instrument. Lockheed Martin Tactical Defense Systems and Naval Research Laboratory combined space age imaging technology and neural net shape classification into the development of LaserNet Fines. LaserNet Fines can be used as a stand-alone analytical instrument, or in conjunction with a full service oil analysis program.
|
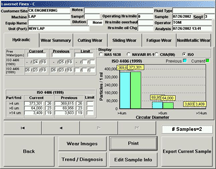 |
Particle Counter
LaserNet Fines processes and stores thousands of images to obtain good counting statistics. Particles are sized directly and put into size bins of 4 - 15 µm. 15 - 25 µm. 25 - 50 µm and greater than 50 µm. The direct imaging capability of this instrument eliminates the need for calibration with a test dust, the exact particle size distribution of which itself may be questionable. Air bubbles are ignored and the laser is powerful enough to process heavily sooted (black) oils.
Sample data output screen with particle counts and number of particles according to wear mode (cutting, sliding fatigue and oxides)
|
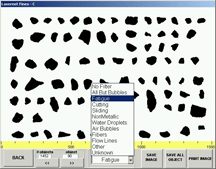 |
Particle Shape Classifier
The second capability of this instrument is shape recognition of all particles greater than 20 µm by using a neural network. An algorithm is used to sort particles into 4 categories, "cutting, fatigue, severe sliding and oxides". The shape recognition software also does a test for circularity so that bubbles and droplets are eliminated.
Sample data particle map output screen. Particles can be selected by wear mode and highlighted for additional size and shape data.
|
.jpg)
|
Operation
A powerful laser transmits a light pulse through a thin (approximately 90 µm thick) cell in which slowly flowing sample is sandwiched between two glass plates. Using magnifying optics, an image of the sample is captured by a CCD video camera and stored in computer memory. Each image is processed with a raster scan analysis to identify individual objects. The objects are then analyzed for maximum size and several shape characteristics which are used to classify particles into mechanical wear classes. Each laser pulse provides a single image frame to be analyzed, and the results of thousands of frames are combined for a complete record of the sample under study.
Sample data output screen with capability to show trends by wear mode and/or particle size ranges.
|
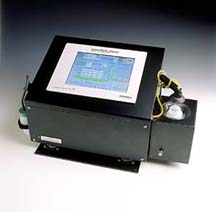 |
Features
o Small size and user friendly interface for shipboard or field deployment
o Algorithms to perform shape analysis, wear particle identification and machine condition assessment.
o Particles counted are greater than 5 µm
o Particles greater than 20 µm are classed by neural network as "cutting, fatigue, severe sliding and oxides"
o Touch screen and LCD user interface
o Provides ISO 4406 cleanliness rating
o Provides NAS 1638 cleanliness rating
o Automatic adjustment for fluid darkness
o Built-in data-base for machine condition trending
LaserNet Fines Military (LNF-M) version with built-in computer.
|
|